Dyeing refers to the process in which dyes are automatically transferred from dye solution to fibers, and evenly, firmly and brightly colored fibers are formed.
One
The basic process of dyeing
According to the viewpoint of modern dyeing theory, the reason why dyes can dye fibers and have a certain fastness on fibre fabrics is that there are various attractions between dye molecules and fibre molecules. The dyeing principle and dyeing process of various dyes are quite different because of the respective characteristics of dyes and fibers. Generalize, but in terms of its dyeing process, it can be roughly divided into three basic stages.
Adsorb
.jpg)
When the fibers are put into the dyeing bath, the dyes first diffuse to the surface of the fibers, and then gradually transfer from the solution to the surface of the fibers. This process is called adsorption.
With the passage of time, the dye concentration on the fiber increases gradually, while the dye concentration in the solution decreases gradually. After a period of time, the dye concentration reaches equilibrium state. The reverse process of adsorption is desorption, and adsorption and desorption exist simultaneously in the dyeing process.
.jpg)
spread
.jpg)
The process of transferring dye from the surface of a fiber to the interior of the fiber.
Due to the adsorption of dyes on the surface of the fibers, the dye concentration on the surface of the fibers is increased, resulting in the difference of dye concentration between the inner and outer surfaces of the fibers. Driven by this concentration difference, the dyes gradually diffuse into the fibers, and eventually make the dyes on the fibers more uniform, so as to achieve the goal of evenness and penetration.
Fixing
Dye fixation refers to the process in which dyes evenly distributed on the fibers after diffusion are fixed on the fibers through dye-mdash; the interaction between the fibers.
dye — the force between fibers.
Chemical force: covalent bond and ionic bond
Physical forces: Fan Dehua force, hydrogen bond and aggregation
Its type and size play a decisive role in the fastness of dyeing.
The above three stages often exist at the same time in dyeing process and can not be completely separated. It is only in a certain period of time that a process is dominant.
Two
color fastness
Dyeing fastness refers to the ability of dyes or pigments to maintain their original color state under the influence of various external factors during the use of dyed fabrics or in subsequent processing.
Dyeing fastness is one of the important quality indicators of dyed products. The dyeing fastness which is easy to fade is low, and the dyeing fastness which is not easy to fade is high. Color fastness depends to a large extent on its chemical structure. In addition, the physical state of dyes on fibers, the degree of dispersion, the combination of dyes and fibers, dyeing methods and technological conditions also have great influence.
External factors causing discoloration or discoloration
Acid, alkali, oxidant, reducing agent and so on during the subsequent processing.
During the use of the sun, washing, friction, sweat, ironing, etc.
Dyeing fastness mainly includes washing fastness, friction fastness, sun fastness, perspiration fastness, ironing fastness, weather fastness, brushing fastness, sublimation fastness, bleaching fastness, alkali fastness, etc. In addition, according to the special uses of products, there are also fastness to seawater and smoke fastness.
Light
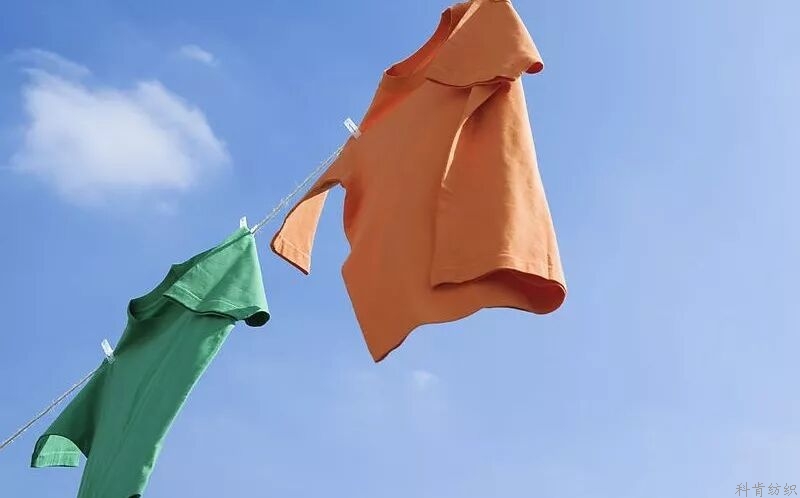
Fading of dyed fabrics is a complex process. Under the action of sunlight, the dyes absorb light energy, and the molecules become extremely unstable in the state of excitation. Some chemical reactions easily occur, which make the dyes decompose and fade, resulting in a larger fading phenomenon of dyed fabrics after sunshine. The fastness of sunlight changes with dyeing concentration, and the light fastness of low concentration is higher than that of high concentration. The fastness to sunlight of the same dye on different fibers is also quite different. For example, the fastness to sunlight of indigo on cellulose fibers is only grade 3, but on wool is grade 7-8. The fastness to sunlight is also related to the aggregation of dyes on fibers, dyeing process and other factors.
The sunlight fastness is divided into 8 grades, the 1 level is the worst, and the 8 grade is the best.
washing
The degree of fading of dyed fabrics after soaping in soap solution under specified conditions, including original fading and white cloth staining.
Fading: the color change of dyed products before and after soaping.
White cloth staining: it refers to the staining of the white cloth soaped with the dyed fabric.
Soaping fastness is related to the chemical structure of dyes and the binding state of dyes to fibers. In addition, soaping fastness is also related to dye concentration, dyeing process and soaping conditions.
The test conditions of soaping fastness vary with the fabric types. The soaping temperatures can be divided into 40 ~C, 60 ~C and 95 ~C. The test samples were tested, washed and dried and then used & ldquo; grey faded sample card & rdquo; graded according to the national standards.
The soaping fastness is divided into five grades and nine grades, among which the first grade is the worst, the fifth grade is the best, and the staining is also divided into five grades and nine grades. The first grade is the most serious staining and the fifth grade is non-staining.
Fastness to washing is the ability to maintain color fastness and discoloration in the soaping process. Two indicators, including original color fading and white cloth staining.
Rubbing fastness DISCOVERY
The friction of dyed fabrics is divided into two types: dry friction and wet rubbing fastness. The former is used for rubbing fabric with white cloth, and the color of white cloth is seen.The latter rubbed the dyed fabric with water 100% white cloth to see the color of the white cloth. Wet friction is caused by external friction and water action, and its wet friction fastness is generally lower than dry friction fastness.
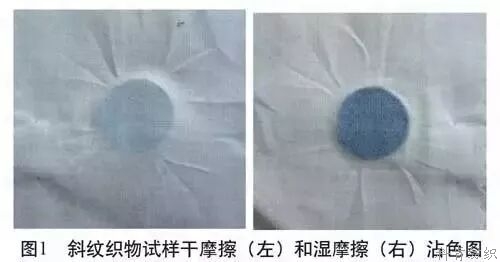
The friction fastness of fabrics mainly depends on the amount of float, the combination of dyes and fibers, and the uniformity of dye penetration. If the dye cooperates with the fiber, its rubbing fastness is higher. The concentration of dyes used in dyeing often affects the rubbing fastness. High dyeing concentration can easily cause floatation, but the rubbing fastness is low.
The rubbing fastness is graded by & ldquo; stained grey sample card & rdquo; according to the five-grade and nine-grade system, the first grade is the worst and the fifth grade is the best.
Fastness to perspiration and fastness to chlorine bleaching
According to the five level nine rating system. To evaluate the dyeing fastness of dyes, textiles should be dyed to a prescribed color concentration to compare. This is because different dyeing concentration will make the measured fastness different. The test methods of dyeing fastness of dyed fabrics should be carried out according to the methods prescribed by the state, and the standards of fastness should also be based on the national standards.
Three
Dyeing method
According to the different objects of dyeing, the dyeing methods can be divided into four categories: ready-made dyeing, fabric dyeing (mainly woven fabric dyeing, knitted fabric dyeing and non-woven material dyeing), yarn dyeing (can be divided into twisted yarn dyeing, bobbin yarn dyeing, warp spindle dyeing and continuous warp yarn dyeing) and bulk fiber dyeing.
Among them, fabric dyeing is the most widely used. Ready-to-wear dyeing refers to the method of dyeing textile materials after they are processed into garments. Yarn dyeing is mostly used for dyed looms and knitted fabrics. Disperse fiber dyeing is mainly used for dyed textile materials.
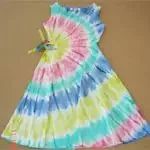
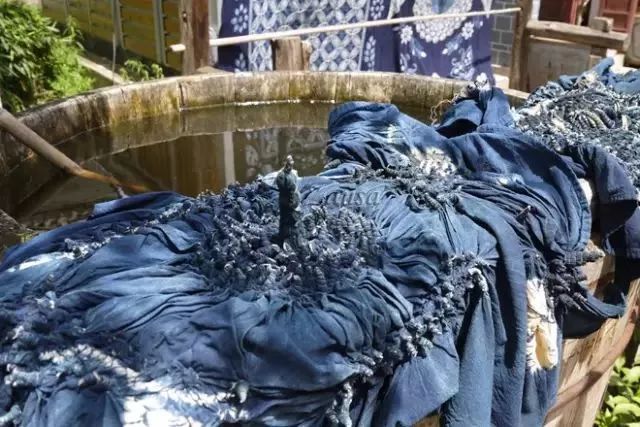
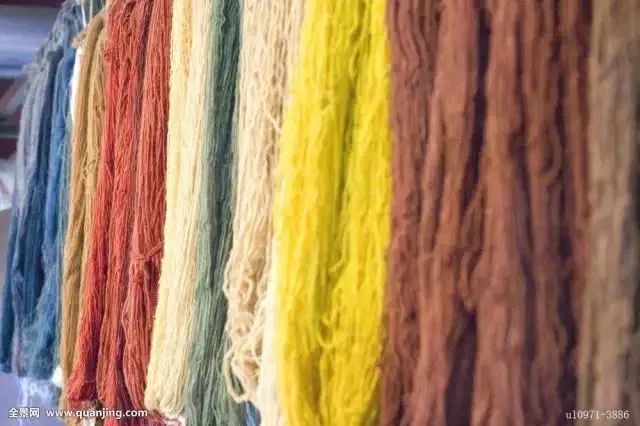

According to the different contact ways of dyes and fabrics (dyeing process), they can be divided into two types: dip dyeing and pad dyeing.
Impregnation
It is a dyeing method in which dyed fabrics are impregnated in dyeing liquor and dyed uniformly by dyeing liquor circulation and relative movement of the dyed fabrics. When dye is disseminated, dyes and dyes can be circulated at the same time or single cycle.
Dipping and dyeing equipment is simple, easy to operate and wide adaptability. It is especially suitable for dyeing loose fibers, yarns, knitted fabrics, wool fabrics and other dyes which can not withstand tension or rolling. Dip dyeing is intermittent production, low labor productivity, suitable for small batch and multi variety production.
Pad dyeing
It is to impregnate the open-width fabric in dyeing solution for a short time, then press the dyeing solution through the roller, squeeze the dyeing solution into the fiber and fabric tissue space, and remove the excess dyeing solution, so that the dyes are evenly distributed on the fabric. After dyeing, the dyed fabric is steamed or roasted to finish the diffusion and fixation of dyes on the fibers. Pad dyeing is mainly used for dyeing of fabrics.
Four
Common dyeing equipment
In the dyeing process, to improve labor productivity and obtain a uniform and firm color without damaging the fiber textiles, first of all, there should be advanced processing methods. In order to select and formulate the dyeing process reasonably according to different products and dyes, the dyeing equipment used must meet the technological requirements.
There are many kinds of dyeing machines, which can be divided into batch dyeing machine and continuous dyeing machine according to the nature of mechanical operation; dyeing methods can be divided into impregnating machine, jigger, pad dyeing machine; according to the state of the dyed fabric can be divided into bulk fiber dyeing machine, yarn dyeing machine, fabric dyeing machine. Reasonable selection of dyeing machinery and equipment plays an important role in improving product quality, reducing production costs and improving production efficiency.
1 continuous rail dyeing machine
Continuous pad dyeing machine is suitable for large-scale continuous printing and dyeing process, with high labor efficiency and low production cost. It is the main dyeing equipment for cotton, chemical fibers and their blended fabrics. According to the different dyes used, the types of continuous pad dyeing machines are different, such as vat dye suspension pad dyeing machine, Nafto dye primer and developer, sulfur dye pad dyeing machine, thermosol dyeing machine, etc.
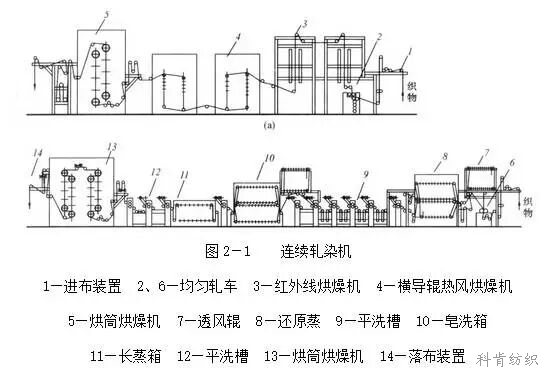
6 Volume dyeing machine
The jigger is a kind of intermittent dyeing machine. According to its working properties, it can be divided into ordinary jigger and high temperature and high pressure jigger.
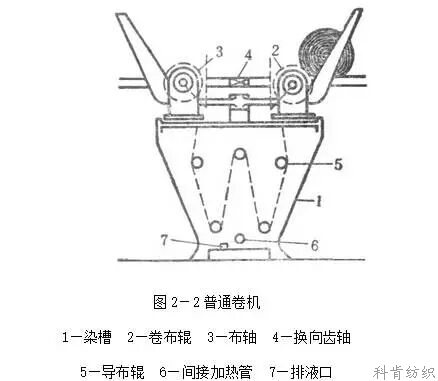
3 overflow and jet dyeing machine
Overflow dyeing machine is a special type of rope dyeing machine. Because the dyed fabric is in a relaxed state, under low tension, soft handle and uniform color, it is used for dyeing synthetic fabrics, warp knitted fabrics and elastic fabrics under high pressure.
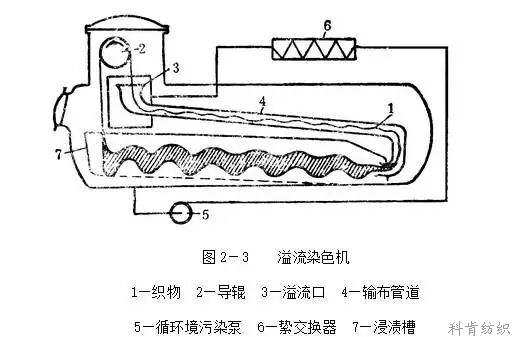
The jet dyeing machine occupies a small area with high output and saves material, power and labor. It has not only high temperature and high pressure type, but also normal pressure type. It can be used not only for synthetic fibers, but also for natural fibers. It can not only be used for dyeing.It can also be used before and after processing.